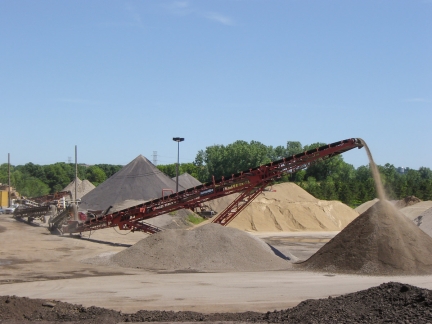
Air emissions
Do I need a permit?
Calculate your potential air emissions. If you exceed the potential emissions thresholds listed in this calculator, you need an air permit:
Federal standard. Is your facility affected by the federal new source performance standard for Nonmetallic mineral processing (Subpart OOO)?
- Fixed plant is larger than 25 tons/hour or your portable plant is larger than 150 tons/hour.
- Plant or equipment was constructed, reconstructed, or modified after August 31, 1983.
What kind of permit do I need?
If you need a permit, most facilities can qualify for the nonmetallic mineral processing general permit:
If you do not qualify for the general permit, it is possible to obtain an air emission registration permit. Use the calculator to determine if your actual air emissions are below the limits of the Registration Option D permit.
If you cannot qualify for either a general or registration permit, then you must apply for another type of air permit. See the Air permit types page for more information.
How do I apply?
Find application forms on the Air permit forms page. Be sure to include the cover page with your packet:
- (8/1/2024)
Compliance tool
Use this compliance calendar as tool to help you stay in compliance with requirements for recordkeeping and reporting:
Dust
Businesses creating fugitive dust should take all reasonable measures to control and keep particles from escaping into the environment (Minn. R. 7011.0150). Minimize dust from blasting, drilling, crushing, conveying, screening, stockpiling, and hauling materials.
- Control dust by using water trucks, windbreaks, on-site speed limits, putting stockpiles in sheltered areas, and planting vegetative ground cover.
- Minimize fugitive dust by limiting the drop heights of materials being transferred to stockpiles, bins, or conveyors; watering dry materials; and leaving empty space at the top of unenclosed aggregate storage bins.
Air permit due dates
Requirement | Due date |
---|---|
Emission inventory fee for previous year | Mailed to permit holders between February and April, due within 30 days |
Emission inventory report | April 1 |
Emission summary review period | Begins in August/September |
January 30 July 30 | |
January 31 | |
For portable facilities: (11/1/2023)
| 48 hours before relocating |
Hazardous waste
You need a hazardous waste identification number if your business produces any amount of hazardous waste.
Businesses generating most types of hazardous waste are required to report annually, pay a fee, and obtain a license for the subsequent year. Facilities in Anoka, Carver, Dakota, Hennepin, Ramsey, Scott, or Washington County are licensed and inspected by their county. Facilities in Greater Minnesota are licensed and inspected by the MPCA. If you produce only small amounts of hazardous waste, you probably qualify as a very small quality generator:
Annual hazardous waste training is required for businesses that generate 220 pounds or more of hazardous waste a month. Learn more: Hazardous waste
Hazardous waste due dates
Requirement | Due date |
---|---|
Hazardous waste generators fee | Mailed to license holders in first quarter, due date on invoice |
License application | Due August 15 for Greater Minnesota businesses; Twin Cities metro businesses: contact your county |
Stormwater and wastewater
Aggregate facilities must have a permit for stormwater and wastewater activities. The nonmetallic mining general permit covers both stormwater and wastewater for the aggregate industry, and is required for process wastewater.
If you have stormwater but no process wastewater, you may still apply for MNG49, which will cover multiple locations under one permit, or you can choose to apply for industrial stormwater general permit for each site.
If you discharge wastewater (non-stormwater) to surface waters that is not authorized by the MNG49 permit, you must obtain an individual NPDES/SDS permit
If you are not sure what permit is right for you, use this chart to help you determine what is most appropriate for your facility and activities:
Water permit due dates
Requirement | Due date |
---|---|
Industrial stormwater general permit quarterly sampling | Jan. 21, April 21, July 21, and Oct. 21 |
Industrial stormwater general permit annual reporting | March 31 |
Discharge monitoring reports for MNG49 general permit for non-metallic mining | Jan. 21, April 21, July 21, and Oct. 21 |
Storage tanks
Most aboveground storage tanks larger than 500 gallons or underground tanks larger than 110 gallons have to be registered with the MPCA. See the storage tank pages for more information.
Environmental review
Contact your local municipality for more information. In general, you may need to prepare an environmental assessment worksheet (EAW) if your operation:
- will disturb more than 40 acres of land.
- has the potential – or is perceived to have the potential – for significant environmental effects. The potential for environmental impact is greater if your operation will be near a wetland, lake, river, residences, or previously undisturbed area such as woods or prairie.
Silica sand
Frac or silica sand mining operations must follow the same regulations as other aggregate operations, plus any local requirements.
Operations with a sand dryer are likely to be subject to federal New Source Performance Standards for calciners and dryers in mineral industries and not eligible for the MPCA non-metallic general air permit or registration air permits. Such operations have to apply for an individual air permit.
If your municipality requires a formal response from the MPCA on whether your operation needs an air permit, an “Applicability Determination” can be used for this purpose.
Other required forms are available on the air permit forms page.
Local regulation
Be sure to check with your county, city, and township to see if they have any additional requirements.
Compliance audit checklists
Beyond compliance
Air
Noise pollution can reflect negatively on your company. Consider ways to lessen noise impact on surrounding properties.
Stormwater
Erosion control. When protective vegetative cover is removed and underlying soil exposed, the risk of erosion greatly increases. Sediment can clog streams, destroy fish spawning beds, and reduce clarity and quality of the water in lakes and ponds. Minimize erosion by practicing the following:
- Leave as much vegetation undisturbed as possible or build vegetative buffer strips.
- Minimize the length of time bare soil is exposed.
- Divert or prevent runoff from flowing across exposed areas.
- Stabilize disturbed soils as soon as possible.
- Slow the runoff flowing across the site.
- Consider using silt fences or sediment traps, or building a sedimentation basin.
Wetlands. When choosing a site and planning your operations, identify nearby wetlands to minimize impact by not disturbing wetlands and not allowing untreated water and runoff to discharge directly into wetlands.
Tanks and chemical storage areas. Inspect for leaks and ensure proper maintenance of fuel tanks and chemical storage areas. Check the containment to ensure it is in good condition and sufficient freeboard is available.
Vehicle tracking. Minimize vehicle tracking of dust onto roadways by regularly inspecting exit roads. Immediately remove tracked dirt and mud from roadways.