Plastics are among several priority materials that need help to make them easier and more profitable to recycle
Could be a staple. Maybe a screw, a nail, a bolt. Whatever it is, any metal that gets into the conveyor line at plastic recycler Poly Plastics in Owatonna will cause havoc.
Usually concealed in pallet wrap or some other plastic used for shipping consumer goods, the metal is incidental — just something the plastic picked up along the way — as Andy Michaletz, the owner of Poly Plastics, describes it. If it makes its way entirely down the line, in a process that takes just seconds, it could jam the extruders at the end of the line or tear up the filters in the extruders.
“It can shut the whole line down and cause tremendous amounts of damage,” Michaletz says.
For that reason, Poly Plastics didn’t accept any post-consumer plastics like pallet wrap, retail bags, or boat wrap for recycling, leaving much of it to head to the landfill. At least, it didn’t until a recycling market development grant from the MPCA, part of an ongoing grant program intended to support and encourage the recycling of plastics and other materials, allowed Poly Plastics to buy a key piece of equipment to expand into that market.
Hurdles for the nurdles
Michaletz’s father started Poly Plastics in 1963 by convincing manufacturers to send him their polyethylene scrap — trimmings, overruns, obsolete items — for recycling and that’s essentially the same core business model Michaletz follows to this day.
Polyethylene, Michaletz says, can be easily recycled via mechanical processes. Found in milk jugs, detergent bottles, and plastic shopping bags, polyethylene is a thermoplastic, which means it just needs the right amount of heat to soften it, then it can be remolded or pushed through an extruder to be turned into pea-sized pellets called nurdles, which manufacturers then use to create new plastic products.
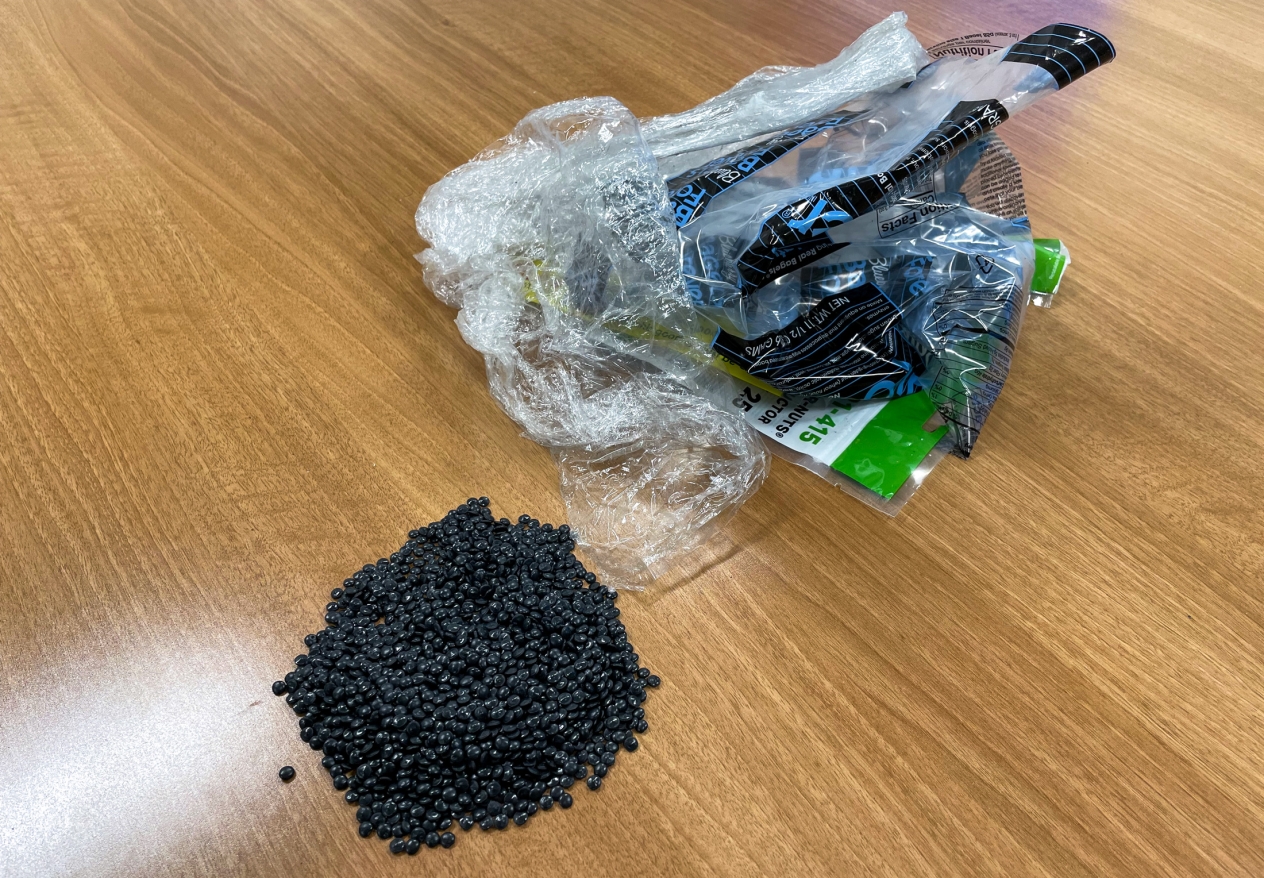
Here in Minnesota, those nurdles typically get turned into plastic drain tiles for farm fields, wood-plastic composites for decking and outdoor furniture, and seat brackets for boats, among other products, according to Wayne Gjerde, the recycling market development coordinator for the MPCA.
“We’re heavy in plastics in Minnesota,” Gjerde says. “A lot of jobs in this state are just a few steps away from somebody who uses recycled plastics.”
Technically, Michaletz says, there’s no limit to the industry’s ability to recycle plastic. But that doesn’t mean everything gets recycled: In Minnesota, only about 10 percent of the 656,420 tons of plastic that gets thrown out becomes new products. Little things like nails and staples can cause recyclers to reject significant sources of plastics. And big things like market economies can make recycling certain items financially unfeasible for recyclers and manufacturers.
“We’re trying to create a balance of recycled materials and products using recycled materials,” he says.
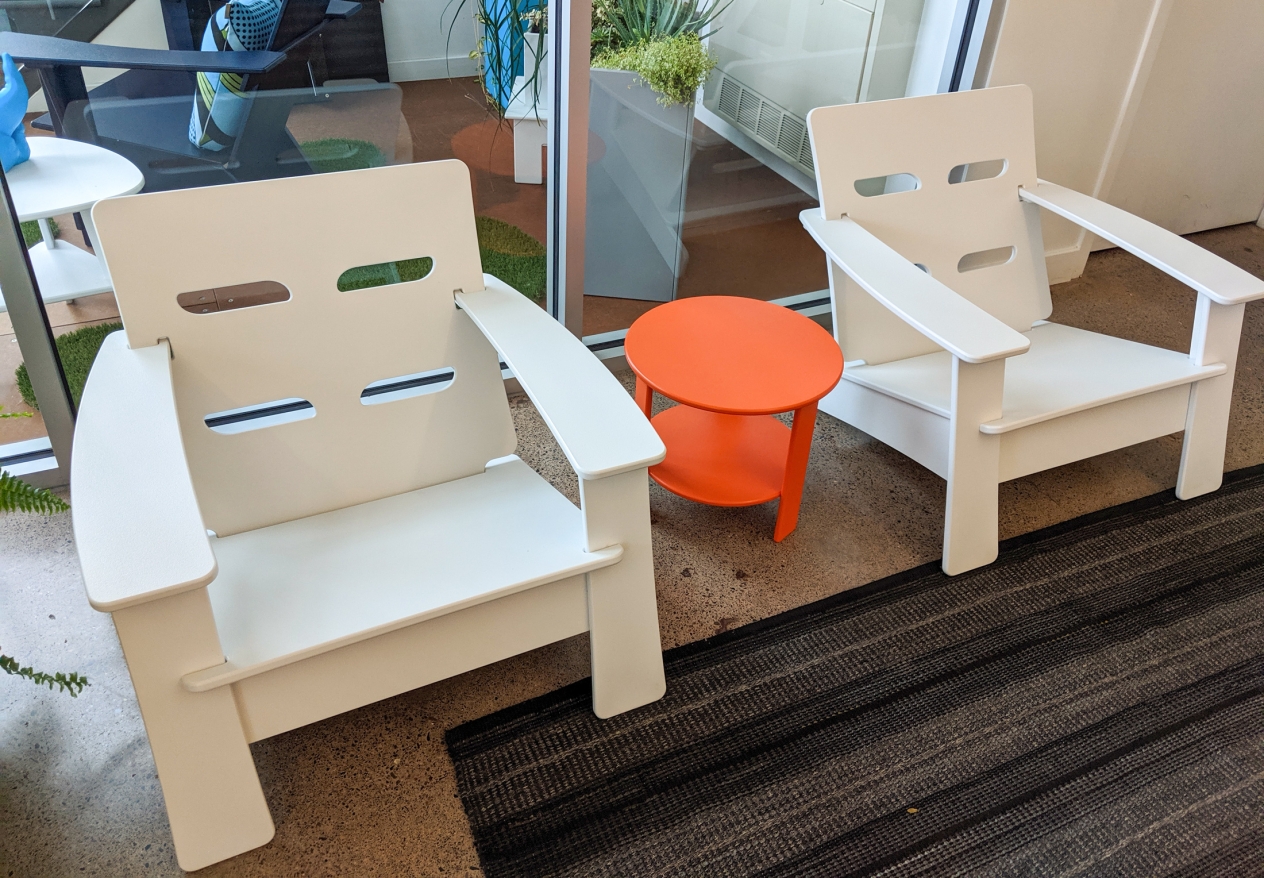
To help strike that balance and eliminate hurdles in the recycling process, the MPCA stepped in with its recycling market development grants that make it more feasible for manufacturers to use recycled materials.
“Without end markets, we don’t have recycling,” says Susan Heffron, an MPCA recycling market development coordinator. “Somebody has to buy that recycled material.”
Key investments for recyclers
The grant program started in 2019 after the Legislature dedicated $800,000 every two years to support it. The MPCA already had a recycling market development program and a revolving loan fund, but the grants allowed the program to expand on those efforts.
While the grants can fund pretty much any activity that diverts recyclable materials from landfills and back into the circular economy, Heffron says that most of the grants have offset the cost of equipment that recyclers need to accept materials they couldn’t previously handle.
“They tell us they can do more, but there’s no way for them to process material with the bottlenecks they have,” she says. “Sometimes it’s just a question of buying a baler — they have all this loose shrinkwrap, but the end market will only take it baled.”
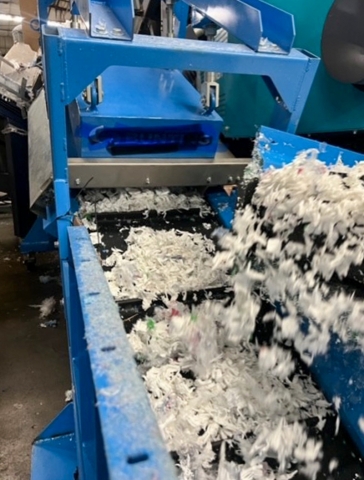
In 2021, the MPCA gave Michaletz $50,000 out of the recycling market development program toward the purchase of a magnetic separator, a machine that plucks those tiny nails and staples from pallet and boat wrap before they hit the extruders. It’s a relatively small piece of equipment for his operation, he says — about the size of a conference table — but it has expanded his business’s capacity to take post-consumer plastic films in addition to the post-industrial plastic films that the company has recycled since the 1960s. In his grant application, Michaletz said he expected to be able to recycle up to 500 tons of additional material every year with the magnetic separator.
That’s not to say the post-industrial plastic recycling market is fully fleshed out, either. In a prior grant round in 2020, the MPCA gave Cosmos-based P.E.C.E. Recycling a $91,165 grant to help fund the purchase of a grinder and shredder to process waste rolls of vinyl tape from 3M.
“It looks like there’s nothing wrong with it,” said Donnie Hopp, the president of P.E.C.E. “You wouldn’t believe that they were incinerating it before.”
With the equipment in place, Hopp now takes in about 675 tons of the tape every year and sends the shredded vinyl off to a company that turns it into garden hose. The cardboard cores at the center of the tape rolls get shredded and sent off to be used for animal bedding.
“I wouldn’t have been able to do this without the grant,” he says. “It’s a tough market.”
Building demand for recycled materials
With the budget surplus in the 2023 legislative session, the MPCA recycling market development program was able to secure a substantial one-time increase for the 2024 round of grants to $5.3 million, which comes just in time to counter a sudden downturn for plastics recyclers.
According to Gjerde, the oil and chemical industries have flooded the plastics market with ethylene resin over the last 18 months, sending prices for virgin plastics plummeting, below the cost of recycled plastic. Lower prices for virgin plastic resin makes it more attractive to manufacturers and, as a result, the recycled plastic market suffers.
“They do this every five years or so, but this is the worst I’ve seen it,” he says.
Michaletz says that his customers tell him every week now that they’re switching from recycled to virgin plastic for their products and that plastic recyclers are folding or bowing out of the industry left and right.
While recycled plastic offers environmental benefits — it requires less electricity to produce and creates fewer greenhouse gases during production — and creates jobs in the state, “it still comes down to the dollars and cents of making the product,” he says. “It’s the right thing to do, but without markets, we’re pushing a rope uphill, we can’t go anywhere with the stuff. We can only compete on cost, and it has to be cheaper. So we need to see some pull, some demand.”
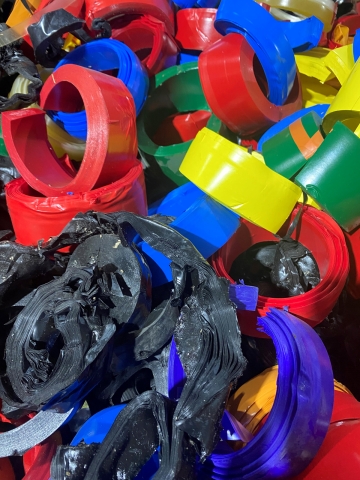
The MPCA is pushing for laws mandating minimum recycled content at the state house, Gjerde says, which could create some of that pull.
Meanwhile, the MPCA has prioritized plastics — including plastic films — for the recycling market development grants, giving any project designed to create demand for recycled plastics greater weight because plastics need that extra help finding their way to end markets, Heffron says.
The more end markets that use recycled material, she notes, the less demand for virgin plastic. The more demand for recycled plastic in Minnesota, the less plastic sent to Minnesota landfills.
“And when we put something in the landfill, it doesn’t generate one cent of economic activity after that,” Gjerde says.
For more information on the MPCA's recycling and other grant programs, visit www.pca.state.mn.us/grants.