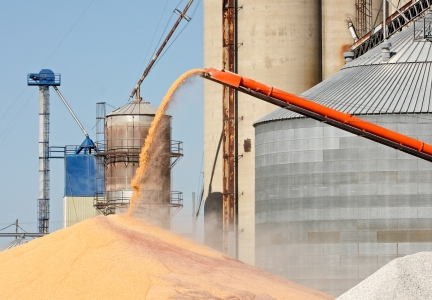
Air emissions
Use the grains and commodities assistance tool to quickly assess if your facility is subject to state rules and to get a summary of requirements and how to comply. This calculator will help you determine if you need an air permit:
-
- Fertilizer mixing plants: Use the 'grain elevator' tabs in the calculator to calculate emissions from granular fertilizer mixing and handling.
If the federal standards don’t apply to you (see below), see the standards of performance for dry bulk agricultural commodity facilities (Minn. R. 7011.1000 to 1015). State rule may require your business to have air emission controls.
- If you use a capture system, the particulate matter must go through control equipment that has a collection efficiency of at least 80% by weight.
- Column dryer screen perforations must be 3/32 inches in diameter or less.
- Emissions from a rack dryer must be filtered by a 50-mesh or finer screen enclosure before discharge to the atmosphere.
Federal permits
Grain elevators: New Source Performance Standards (NSPS) apply if the facility's unloading stations, loading stations, grain dryers, or grain handling operations have been constructed, modified, or reconstructed since August 3, 1978, and the elevator has a permanent storage capacity of about 2.5 million bushels or more (or, for elevators located at a wheat flour mill, wet corn mill, dry corn mill for human consumption, rice mill, or soybean oil extraction plant, a permanent storage capacity of about 1 million bushels or more). See the file below for a summary of the requirements.
Feed mills may be subject to the National Emission Standard for Hazardous Air Pollutants (NESHAP) for prepared feeds manufacturing (40 CFR Part 63, Subpart 7D) if they use additives or premixes containing chromium or manganese. The below EPA fact sheet summarizes the regulation and its requirements.
Fugitive dust
With either standard, you must unload, handle, clean, dry, and load commodities in a way that minimizes fugitive dust and prevents avoidable amounts of dust from becoming airborne, including dust from your driveway.
You cannot operate a grain elevator in such a way that it creates a public nuisance. You must:
- clean up commodities spilled on the driveway and property.
- maintain air pollution control equipment in proper operating condition and use them as designed.
Hazardous waste
You need a hazardous waste identification number if your business produces any amount of hazardous waste.
Businesses generating most types of hazardous waste are required to report annually, pay a fee, and obtain a license for the subsequent year. Facilities in Anoka, Carver, Dakota, Hennepin, Ramsey, Scott, or Washington County are licensed and inspected by their county. Facilities in greater Minnesota are licensed and inspected by the MPCA. If you produce only small amounts of hazardous waste, you probably qualify as a very small quality generator:
See the Hazardous waste identification and management page for information on managing specific types of hazardous waste, such as antifreeze, lead-acid batteries, solvents, waste tires, used oil, and much more.
Annual hazardous waste training is required for businesses that generate 220 pounds or more of hazardous waste a month. See Step 9 Train your employees in the summary of hazardous waste requirements.
Hazardous waste due dates
Requirement | Due date |
---|---|
Hazardous waste generators fee | Mailed to license holders in first quarter, due date on invoice |
License application | Due August 15 for Greater Minnesota businesses; Twin Cities metro businesses: contact your county |
Stormwater
Generally, grain elevators that buy, sell, or market grain are likely to be exempt from the industrial stormwater permit. "Storage only” facilities, feed mills, and fertilizer mixing plants must obtain a permit. Grain elevators that make most of their revenue from grain but also mix fertilizer do not need an industrial stormwater permit. More information and application forms are on the industrial stormwater permit page.
Tanks
If you store gasoline, diesel, kerosene, or anything else in a tank, be sure you are meeting tank requirements. The MPCA aboveground and underground storage tank pages have more information.
Local regulation
Be sure to check with your county, city, and township to see if they have any additional requirements.
Beyond compliance
Common complaints about grain elevators are about dust and “bees wings” from the grain itself and dust from trucks driving on gravel roads. Whether or not you need any permits, the ideas and practices listed below can help you be a good neighbor by reducing dust, which also benefits your employees.
Communication
- Provide your community with a way they can contact you directly if they have a complaint.
- If you have had a wet fall or a bumper crop year, let your community know you will be running the dryer more than usual and what that will mean for them.
- Rural elevators, let your neighbors know when the harvest is about to start and what hours during the day you will be loading and unloading grain. Because the elevator is quiet most of the year, people may surprised by the increased noise and traffic, especially if they are new neighbors.
- Let neighbors know if you will be conducting particularly noisy operations and how long you expect it to last.
Grain unloading and loading (dump pits and loadouts)
- A primary source of dust is a falling stream of grain hitting a receiving pit. Allow the grain to form a cone around the receiving grate (known as “choke unloading”) to decrease the distance the grain falls.
- Induced draft fans in dump pits must have a capacity of at least 50 cfm/sq. ft. of airflow at the effective grate surface (the grate area through which air passes during unloading).
- Enclose the receiving area as much as possible. Aim for a receiving shed with closed doors at both ends. A receiving shed with no doors (or doors always open) may create a “wind tunnel” effect that is worse than no shed at all. Alternately, consider curtains or a shroud around the receiving pit.
- Prevent grain from falling as much as possible at loadout. Use dead boxes, socks, or drop-down spouts or sleeves that extend at least six inches below the sides of the receiving container to minimize grain free-fall distance.
- Restrict the flow of the grain when the receiving container is empty or only partly full.
- Consider wind speed and direction. Limit grain handling when the wind will cause neighbors to receive excessive amounts of dust or chaff.
- Conduct grain oiling at the dump pit before transferring to bin storage. Check that the oil is dispersed well. As little as ½ gallon of oil per thousand bushels of grain can reduce dust by up to 80%.
- If storing grain in outdoor piles, store for the shortest amount of time possible and keep piles tarped.
Grain dryers
- Inspect dryer screens before each dryer start-up.
- Do not exceed the manufacturer’s recommended capacity for the amount of grain passing through the dryer.
- Enclose grain inlets and outlets to dryers, and enclose as much of the dryer as is practical.
- Double-check that column dryers have screen perforations of 0.094 inch (3/32 inch) or less.
- Double-check that rack dryers have a maximum screen filter size of 50 mesh.
- If it is time to buy a new dryer, consider one that captures the “bees wings.” In general, cross-flow column dryers create less dust and “bees wings” than rack dryers. But if your rack dryers have only a couple of exhaust points, you could add pollution control devices.
- Running your dryers cleanly and efficiently will also help you save energy and money: Low Cost Energy Conservation: Grain Dryers.
Grain-handling equipment
For equipment such as bucket elevators or legs, scale hoppers, conveyors, turn heads, scalpers, cleaners, trippers, and headhouse and other structures:
- Keep grain handling equipment clean and in good condition.
- Enclose or seal grain handling equipment.
- Control the speed of equipment; keep conveyor belts at the minimum speed necessary.
- Use aeration fans as little as possible when loading grain into storage bins.
- Locate and configure equipment so the building helps block windblown dust.
- When you buy new cleaning and processing equipment, choose dust-tight equipment, lip-type shaft seals for bearings on conveyors and other equipment housings, and flanged inlets and outlets for spouting, transitions, and miscellaneous hoppers.
General maintenance
- Clean up indoor and outdoor areas such as floors, roofs, decks, yards, ditches, and curbs to prevent accumulation of chaff and dust that can blow around. Clean up any grain spills on your driveway or access roads.
- Water unpaved roadways or traffic areas to minimize dust to the air.
See the Beyond compliance page for more information on reducing waste and saving money in your business.